Principles of the SPS Process
The SPS process is based on the electrical spark discharge phenomenon: a high energy,
low voltage spark pulse current momentarily generates spark plasma at high localized temperatures,
from several to ten thousand ℃ between the particles resulting in optimum thermal and electrolytic
diffusion. SPS sintering temperatures range from low to over 2000 ℃ which are 200 to 500 ℃ lower
than with conventional sintering. Vaporization, melting and sintering are completed in short periods
of approximately 5 to 20 minutes, including temperature rise and holding times.
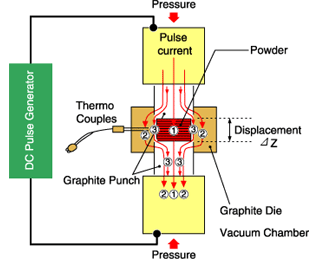 |
ON-OFF pulsed current path |
Mechanism of the SPS Process
The SPS process concentrates high energy pulses at the point of intergranular bonding
offering significant improvements over conventional hot-press and hot isostatic press
sintering. Now, a look at the mechanism of neck formation during the SPS process.
We have already explained under Principles that when spark discharge appears in the
gap between the particles of a material, a local high temperature state of several to
ten thousand ℃ momentarily occurs. This causes vaporization and the melting of the
surfaces of the powder particles during the SPS process; constricted shapes or “necks”
are formed around the contact area between the particles. These necks gradually develop
and plastic transformation progresses during sintering, resulting in a sintered compact of
over 99% density.
Since only the surface temperature of the particles rises rapidly by self-heating,
particle growth of the starting powder materials is controlled. Therefore, a precision sintered compact
is manufactured in a shorter time. At the same time, bulk fabrication of particles with amorphous
structure and nano-crystallization formation are now possible without changing their characteristics.
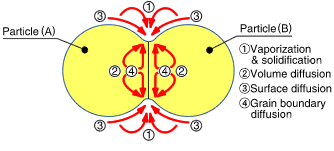 |
Metarial Transfer Path Model During Sintering |
 |
Neck Formation |
Mechanism of the SPS Process
Conventional electrical hot press processes use DC commercial AC power, and the mail factors promoting sintering
in these processes are Joule heat generated by the power supply (l
2R) and the plastic flow of materials
due to the application of pressure.
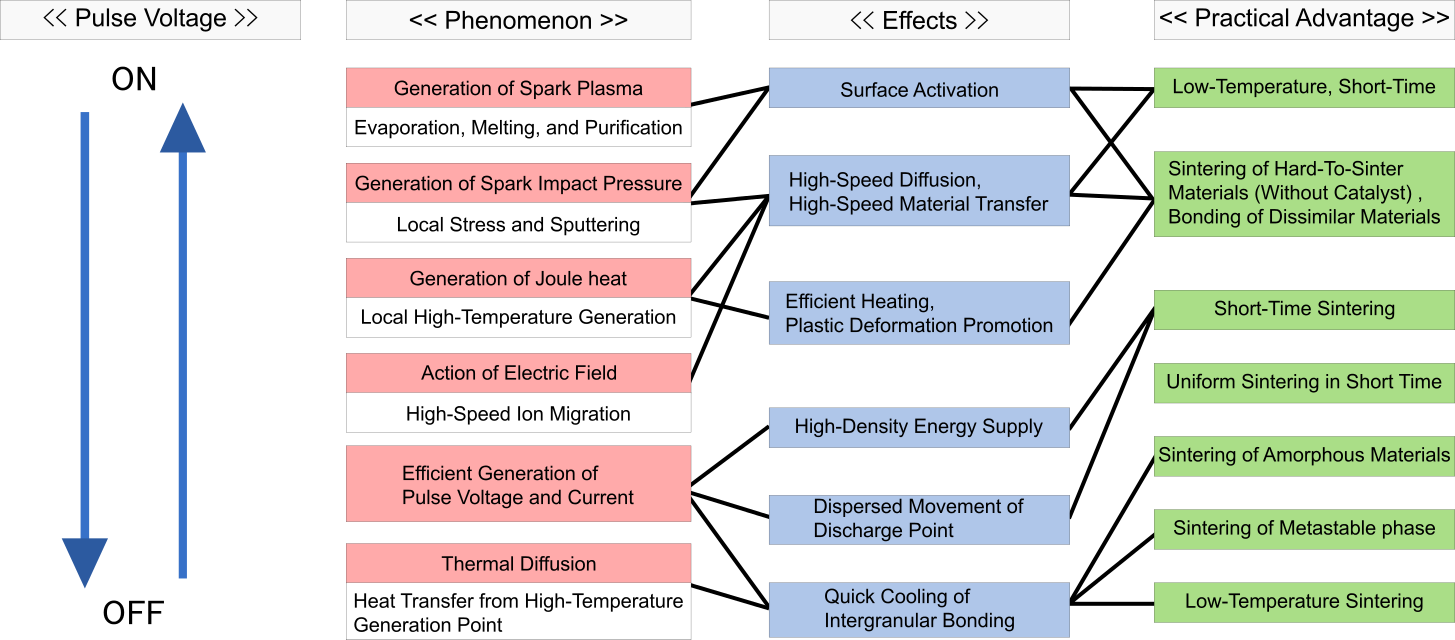 |
Effects of ON-OFF DC Pulse Energizing |
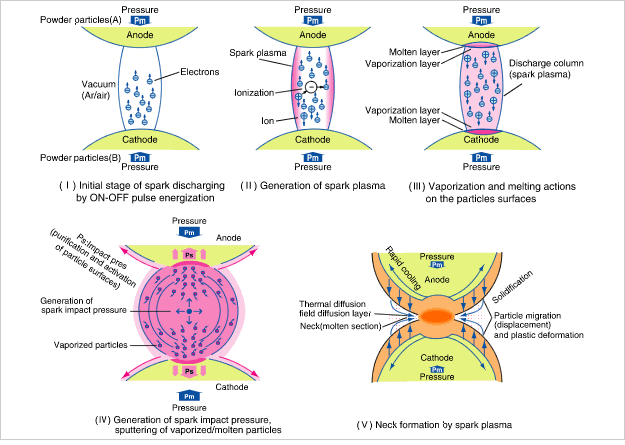 |
Basic Mechanism of Neck Formation by Spark Plasma |